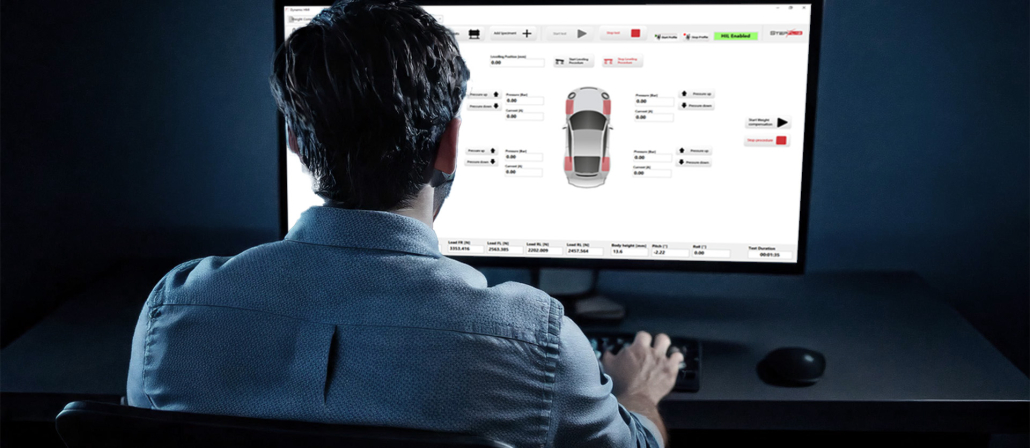
Hardware-in-the-Loop (HIL) simulation is a critical method that allows engineers to test and validate control systems in a safe and controlled virtual environment, without relying on physical prototypes. By simulating a real-world system in real time, HIL enables developers to integrate actual hardware with a virtual model, accelerating development, reducing costs, and increasing safety. This technique is especially useful in complex systems where errors during real-world testing could be expensive or even hazardous.
Originally adopted in industries like aerospace and automotive, HIL has since expanded to sectors such as energy, communications, medical devices, and robotics. As embedded systems become more advanced and interconnected, the need for reliable, repeatable testing is greater than ever. HIL provides engineers with the ability to perform rigorous, high-fidelity tests under a variety of conditions, all from the safety of a simulation.
At its core, HIL simulation involves connecting a physical controller or hardware system to a real-time virtual model that simulates the system it is designed to control. This “loop” allows engineers to test the control algorithms as if they were interacting with the real-world system, but without the need for the actual hardware. The system’s components interact with the simulation via input and output interfaces, creating a seamless integration between the virtual and physical environments.
A typical HIL setup consists of three main components:
In practice, HIL systems allow developers to replace certain components of a system with virtual models, gradually integrating more real-world hardware as development progresses. For example, in testing an automotive ECU, the dynamics of an engine might be simulated in software, while the ECU hardware interacts with the simulated model, as it would in a real car. This setup enables engineers to validate control systems early in the development cycle without risking damage to expensive or sensitive equipment.
1. Cost-Effective Development
One of the most significant advantages of HIL simulation is cost savings. Testing real-world prototypes, particularly in industries like aerospace or automotive, can be prohibitively expensive. The cost of building, maintaining, and operating physical test environments, not to mention the risk of damaging expensive hardware during testing, can quickly add up. HIL eliminates much of this expense by allowing testing to occur in a virtual environment.
For example, in jet engine development, using a physical engine for each test is not only expensive but also impractical. A single jet engine can cost millions of dollars, while a high-fidelity HIL system designed to simulate the entire engine can be built for a fraction of that cost.
2. Improved Safety
Safety is a top concern in testing high-risk systems like automotive braking systems or flight control systems. Traditional testing methods require using physical prototypes, which can be risky if a malfunction occurs during testing. HIL removes this risk by allowing critical systems to be tested in a controlled, simulated environment where failures can be analyzed without any real-world danger.
For instance, in aerospace applications, HIL is used to test flight control systems in scenarios that would be too dangerous to replicate in real life. Engineers can simulate critical failures or extreme conditions to ensure the system behaves correctly without risking damage to equipment or harm to test pilots.
3. Flexibility and Repeatability
HIL simulations offer unparalleled flexibility in testing. Engineers can run tests in various conditions, tweaking parameters on the fly without the need to physically modify hardware or reconfigure test setups. This allows for quick iterations and comprehensive testing under multiple scenarios, including edge cases that might be too difficult or risky to test in real life.
Furthermore, HIL tests are highly repeatable, meaning the same test can be performed under identical conditions multiple times. This is particularly useful in industries like automotive, where regulatory requirements demand rigorous validation processes before a new system can be deployed.
4. Faster Development Cycles
Traditional testing methods often slow down development due to the time required to build physical prototypes and set up real-world test environments. HIL enables parallel development, where software and hardware teams can work simultaneously. Control algorithms can be tested and refined in the virtual environment, even before the physical hardware is available.
For example, automotive companies can test the performance of new ECUs in a simulated driving environment long before a prototype vehicle is ready. This not only accelerates time-to-market but also helps identify and fix issues earlier in the development process, reducing the likelihood of costly redesigns later on.
HIL test system: Electrodynamic machine and Software by STEP Lab, and hardware by VI-Grade.
Hardware-in-the-Loop (HIL) simulation is a game-changing tool in the world of engineering and development, offering benefits that range from cost savings to increased safety and flexibility. By creating a bridge between virtual simulations and real-world hardware, HIL allows for more rigorous testing, faster development cycles, and the ability to explore a wider range of scenarios than ever before.
As industries continue to evolve and embrace more complex embedded systems, the role of HIL will only grow. Whether it’s testing autonomous driving systems, ensuring the safety of flight controls, or validating renewable energy systems, HIL is proving to be an invaluable tool in creating safer, more reliable technologies.
What does HIL mean?
HIL stands for Hardware-in-the-Loop, a testing method that integrates real hardware components with a simulated virtual environment. The goal is to test and validate control systems in real-time by simulating the behavior of the rest of the system, allowing the hardware to interact as if it were in a real-world scenario.
What is HIL used for?
HIL is used to test and validate control systems early in the development cycle. It’s particularly useful in industries like automotive, aerospace, and energy, where complex systems like electronic control units (ECUs), sensors, or actuators need to be tested under realistic conditions. It allows engineers to run tests on individual components without the need for fully assembled prototypes, ensuring that the system will perform correctly in real-world conditions.
What are the components of the HIL system?
A typical HIL system consists of three main components:
Why do we need HIL testing?